Lessons Learnt: Onboard Familiarisation: Mis-Timed
The inspection of an accommodation elevator onboard a semi-submersible mobile offshore drilling unit (MODU), while she was at anchor, resulted in fatal injuries to one of the 2 technicians involved. The incident occurred in good weather and during routine working hours. The technicians, who had been working onboard the MODU since its construction about 4 years ago, held appropriate industrial certifications and was reported to have the technical knowledge to perform their task of maintaining the elevator.
Both technicians were tasked to repair the faulty doors of the cargo elevator. Following the Safety Management System (SMS) procedures onboard, a Permit to Work (PTW) and a Job Safety Analysis (JSA) were carried out and approved for the repair of the cargo elevator. As the cargo elevator was of the same make as the accommodation elevator, the technicians intended to inspect the accommodation elevator to make a diagnosis before working on the repair.
To inspect the elevator, the mode selector was switched from ‘Auto mode’ to ‘Inspection mode’ so as to allow local control of the elevator movement. The elevator was locked at Deck 2 lift landing. After about 10 minutes of the inspection, one of the technicians climbed back on the roof of the cage to re-engage the elevator from ‘Inspection mode’ to ‘Auto Mode’. The 2nd technician then entered the elevator. Subsequently, the 1st technician manually closed the sliding doors at the deck landing and those of the elevator car.
After both the sliding doors were closed, the elevator began to move upwards and came to an abrupt stop. The 2nd technician who was inside the elevator saw blood seeping through the top section of the door. An alarm was raised and the 1st technician was found unconscious on the roof of the elevator car with his head lodged between the front edge of the elevator and the elevator landing frame. Shipboard medics declared the technician dead and autopsy report revealed death due to traumatic skull and face injuries.
Elevator’s design
- The elevator had a selector switch which, when put in ‘Auto mode’, would trigger the elevator’s initialisation sequence (i.e. the elevator will move to the next higher level before going down to a lower level where the elevator car doors will be opened for 10 seconds, ready on standby to be called from any landing).
- The elevator car doors provided a safety barrier for the elevator to move in ‘Auto mode’. The elevator was designed not to move in this mode if these doors remained open.
Why did it happen?
- The safety barrier provided by the elevator car door to prevent operation of the elevator when in ‘Auto mode’ was lost when the car elevator door was closed. As the 2nd technician became a passenger in the elevator, the 1st technician who was now positioned on top of the elevator car was subject to movements of the elevator as per the initialising sequence.
- Following the company’s SMS, the PTW and JSA were only completed for the repair of the cargo elevator but not for the inspection of the accommodation elevator. If the PTW and JSA had been carried out for the accommodation elevator, it would have raised the safety awareness of both technicians to the hazards associated with the elevator, mitigating the risk involved.
Safety Issues
- Although the company’s SMS provided for a PTW and JSA to be completed, on this occasion, an inspection was not considered relevant for such a PTW and JSA to be carried out for the accommodation elevator.
- Even though the technicians had been carrying out maintenance for the elevator on the MODU since its construction, it appeared that they were not fully familiar with the equipment. Particularly, on the risks associated with the initialisation sequence of the elevator after completion of an inspection/repair
- This incident also highlights the importance of ensuring appropriate and timely onboard familiarisation.
Safety Recommendations
- It is recommended that companies revise their SMS to ensure that the PTW and JSA’s are completed for every inspection and maintenance job, especially those involving elevators.
- Refresher training for elevator maintenance and to raise crew awareness to ensure adequate safeguards against all identified risks, in particular on signage and warning signs of the elevator initialisation sequence should be included in the on-board familiarisation.
Lessons Learnt: Non-Compliance with Maker’s Instructions- A Costly Decision
What happened?
A junior engineer was tasked by the 2nd engineer to troubleshoot the alarm condition of an incinerator while the gas carrier was at sea. Having been shown how to rectify the fault in the past (i.e. removal of stuck plastic causing the alarm condition from the top feeding door of the incinerator), the junior engineer continued his assigned task on the second day without any supervision.
About 40 minutes later, the junior engineer’s body was found by the engine crew trapped in between the incinerator sluice and the frame of chamber. The body was stuck from the chest and neck upwards with his head inside the chamber. Initial attempts to remove his body from the location were unsuccessful until one of the engineers shut off the activation air for the sluice. There were no eye-witnesses to the incident. Onboard Cardio Pulmonary Resuscitation (CPR) performed by the crew was futile and the junior engineer was declared dead after consulting Radio Medical Advice.
Why did it happen?
It appeared that the junior engineer had initiated a different approach compared to what was shown to him previously. He had attempted to remove the plastic by accessing it from the sluice door instead of the top charging door. To do this, he opened the inspection hatch of the chamber and forced the solenoid valve for the air on the sluice door, using pliers while it was in an energised status with his body positioned inside the chamber. Once the plastic was removed, the sluice opened outward and his body was stuck in between the frame and the sluice door.
Safety Issues
- There was insufficient supervision on work performed by a junior engineer for a task that posed risks and hazards.
- Even though the shipboard instructions for incinerator maintenance were displayed at the location near the incinerator, none of the instructions were complied with at the time of the incident.
Safety Recommendations
- It is recommended for companies to revise their Safety Management System (SMS) to ensure that appropriate Risk Assessments are conducted by senior shipboard staff and that less experienced junior shipboard staffs are properly appraised on the workplace hazards before work is carried out by them. Ensuring adequate supervision where necessary, should form a part of this risk assessment.
- The SMS should also ensure that personnel onboard are adequately familiarised with the onboard equipment(s).
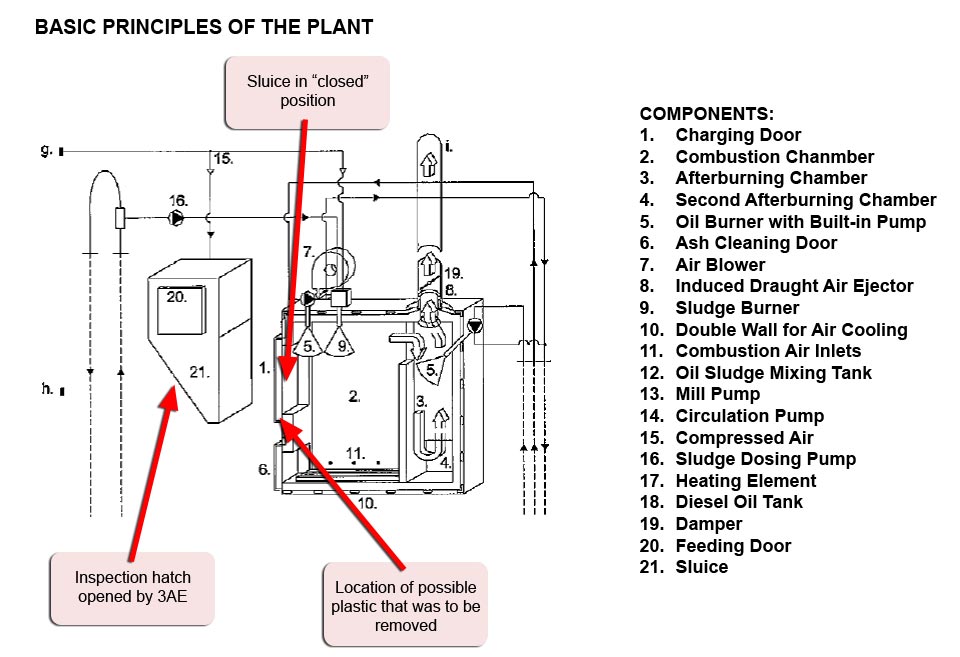
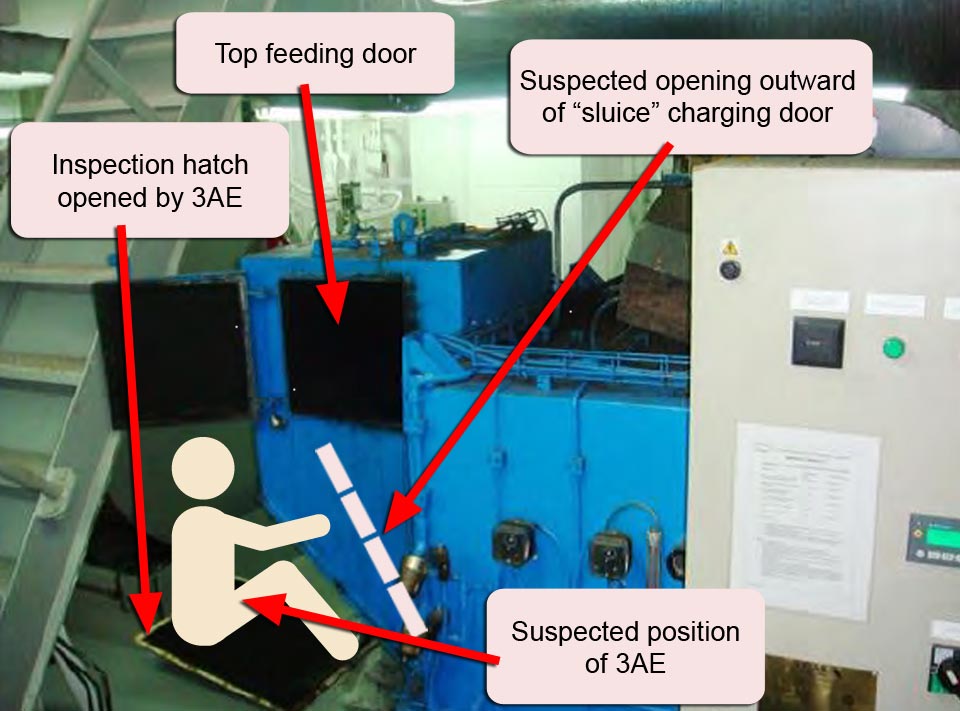